Diseñado específicamente para la realización de ensayos civiles, lleva prestando servicio desde hace más de 20 años a clientes nacionales e internacionales líderes en su sector.
El Túnel Aerodinámico para ensayos civiles del Instituto Tecnológico y de Energía Renovables (ITER), es una infraestructura, perteneciente al Departamento de Energía Eólica y gestionada y operada por la Unidad de Robótica, que permite la realización de ensayos para conocer la respuesta aerodinámica de un objeto en determinadas condiciones de viento.
Diseñado específicamente para la realización de ensayos civiles, aumentando su eficiencia y versatilidad, supone un gran avance para la investigación aerodinámica en múltiples campos. El Túnel de Viento del ITER fue el primer túnel de estas características instalado en Canarias y lleva más de 20 años prestando servicio a clientes internacionales líderes en su sector como Airbus, Altran, Renfe, Axial, etc…
Su diseño y construcción, junto con la planta de potencia y regulación, lo convierten en un túnel altamente competitivo en costes y prestaciones y adecuado para una gran variedad de aplicaciones: ingeniería civil, arquitectura, energías renovables, ingeniería agrícola y principalmente ingeniería aeronáutica.
¿Cómo funciona?
Para la ejecución de un ensayo aerodinámico en el túnel de viento se sitúan objetos reales o maquetas a escala de los mismos en la cámara de ensayos y mediante un software de control se opera un conjunto de ventiladores de gran potencia que permiten simular diferentes condiciones de viento y así observar el efecto real que éste ejerce sobre ellos.
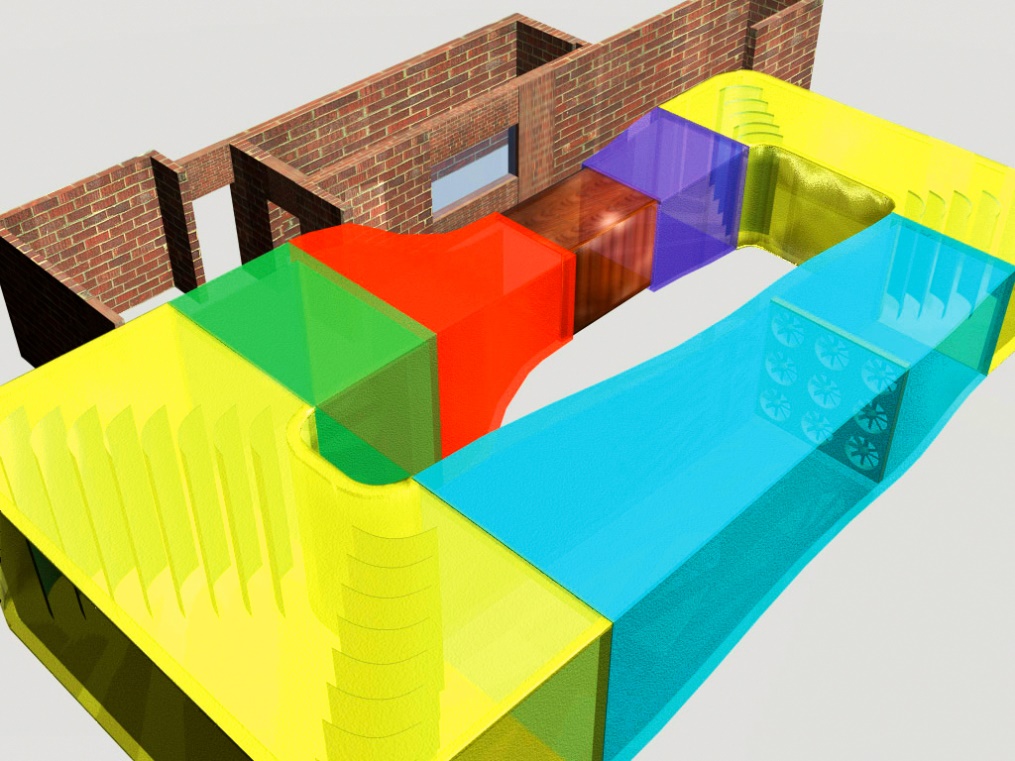
Imagen 1. Esquema del túnel de viento de ITER.
El personal especializado de la Unidad de Robótica participa en las diferentes etapas de la realización de campañas de ensayos aerodinámicos en el Túnel de Viento de ITER: diseño y modelado de prototipos, fabricación e integración y calibración y operación del túnel.
Diseño y modelado
La cámara de ensayos del túnel tiene una sección de 2×2 m y esto restringe el tamaño máximo del objeto a ensayar, por lo que normalmente se requiere de la fabricación a escala de un modelo del mismo. A partir de las especificaciones del modelo tridimensional aportado por el cliente, se determina la metodología de fabricación del modelo a escala del objeto sobre el que se quiere realizar el ensayo, decidiendo el tipo de material a utilizar (madera, fibra de vidrio, impresión 3D, aluminio, etc…), la maquinaria y los útiles necesarios para su fabricación.
Una vez definida la metodología, comienza el proceso de modelado que transforma la información del modelo tridimensional a los requisitos del equipamiento a emplear. Por ejemplo, en el caso de optar por una metodología de fabricación en capas de madera, será necesario rebanar el modelo y generar cada una las capas para posteriormente generar los archivos de programación de la cortadora de control numérico.
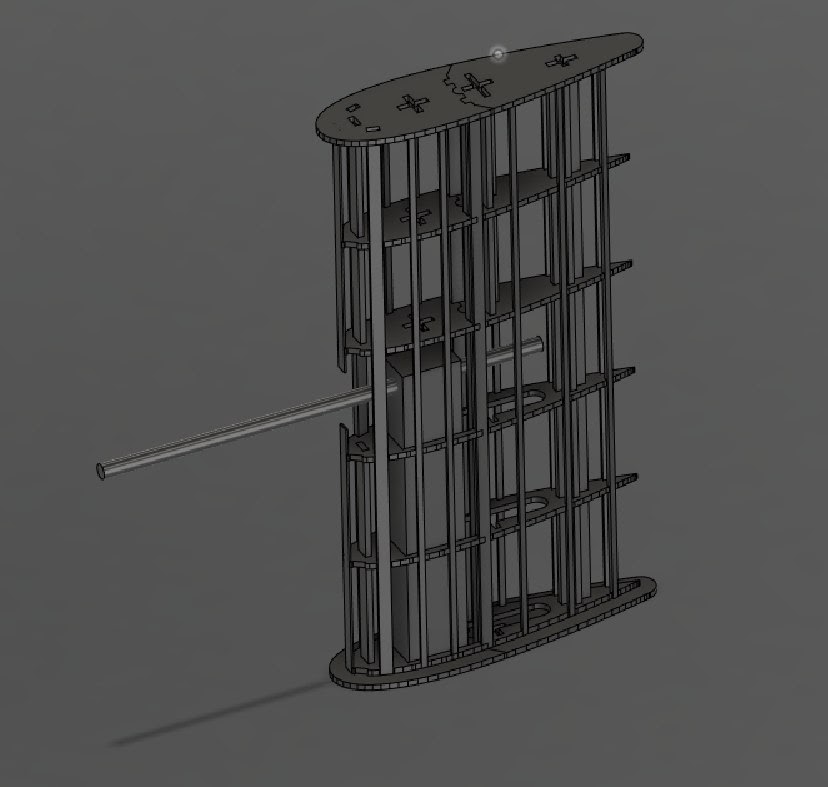
Imagen 2. Modelo 3D para fabricación con costillas de madera, en concreto de una carena para soporte trasero.
Durante este proceso se emplean técnicas de fabricación de gran precisión que nos permiten cumplir con los requisitos y tolerancias de error que se definen en la campaña de ensayos.
Fabricación y Acabado
Para la fabricación se dispone de diferentes tipos de maquinaria como, por ejemplo, máquina de corte por control numérico (CNC), máquina de corte láser, máquina de corte de espuma, varias impresoras 3D y herramientas de taller como taladros de precisión, sierras y otros utensilios.
Una vez se dispone de los materiales, útiles y archivos de modelos para fabricación por control numérico, láser o impresión 3D se comienza la fabricación del modelo. En el caso de una metodología de fabricación en madera se mecanizan todas las piezas de manera individual, programando para ello la máquina CNC, y una vez completado el corte se procede al ensamblaje de las piezas.
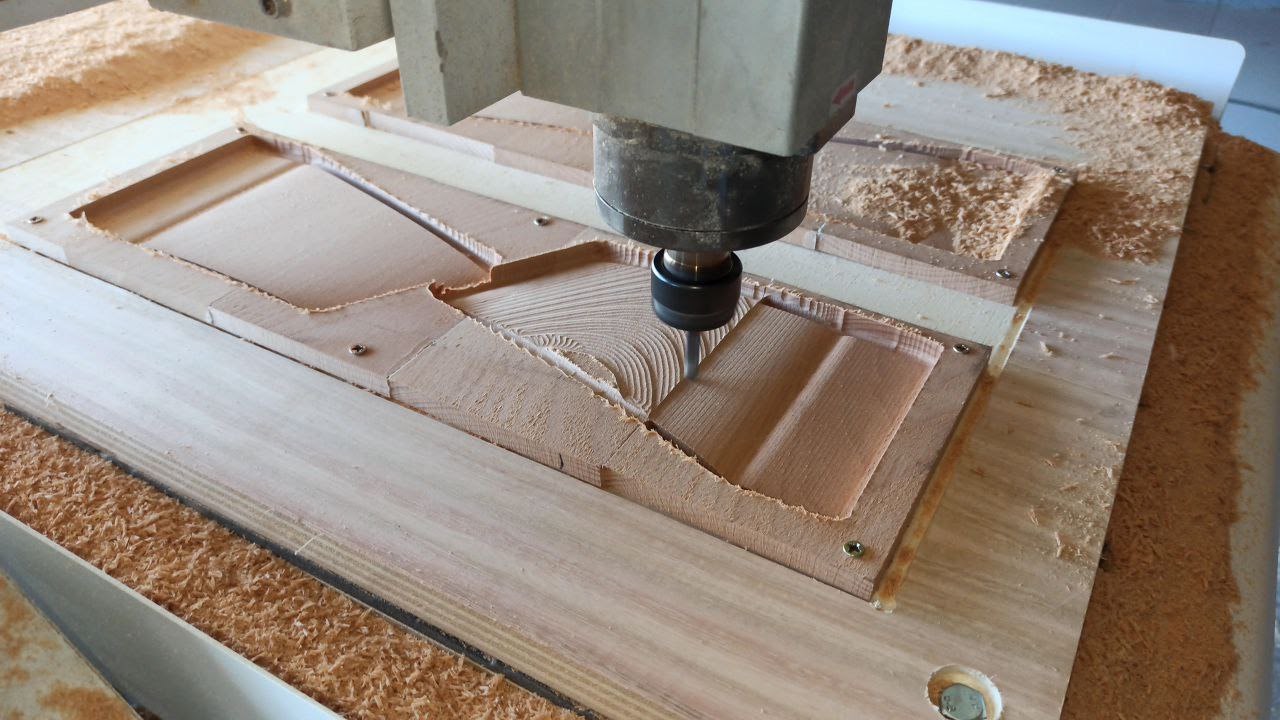
Imagen 3. Mecanizado por máquina de corte por control numérico (CNC) de modelo en madera de haya.
Con el modelo fabricado quedaría la fase de acabado del modelo, crítica en el proceso, ya que es la que condiciona el cumplimiento de los criterios de rugosidad del modelo a ensayar, un parámetro clave en muchos ensayos aerodinámicos. Por ejemplo, para el acabado de las piezas en el caso de fabricación con madera, se comienza con un lijado progresivo disminuyendo el grano de la lija y se da un acabado de pintura que finalmente también se pule para eliminar posibles irregularidades.
Integración y Calibración
El siguiente paso tras concluir la fabricación del modelo es su integración en el túnel de viento. En base a los criterios y parámetros que el cliente quiera obtener durante la realización de los ensayos, los técnicos de operación del túnel montan el modelo sobre un soporte que a su vez está fijado a la balanza y que permite observar variaciones muy pequeñas de las fuerzas que aplica la corriente de aire sobre el modelo.
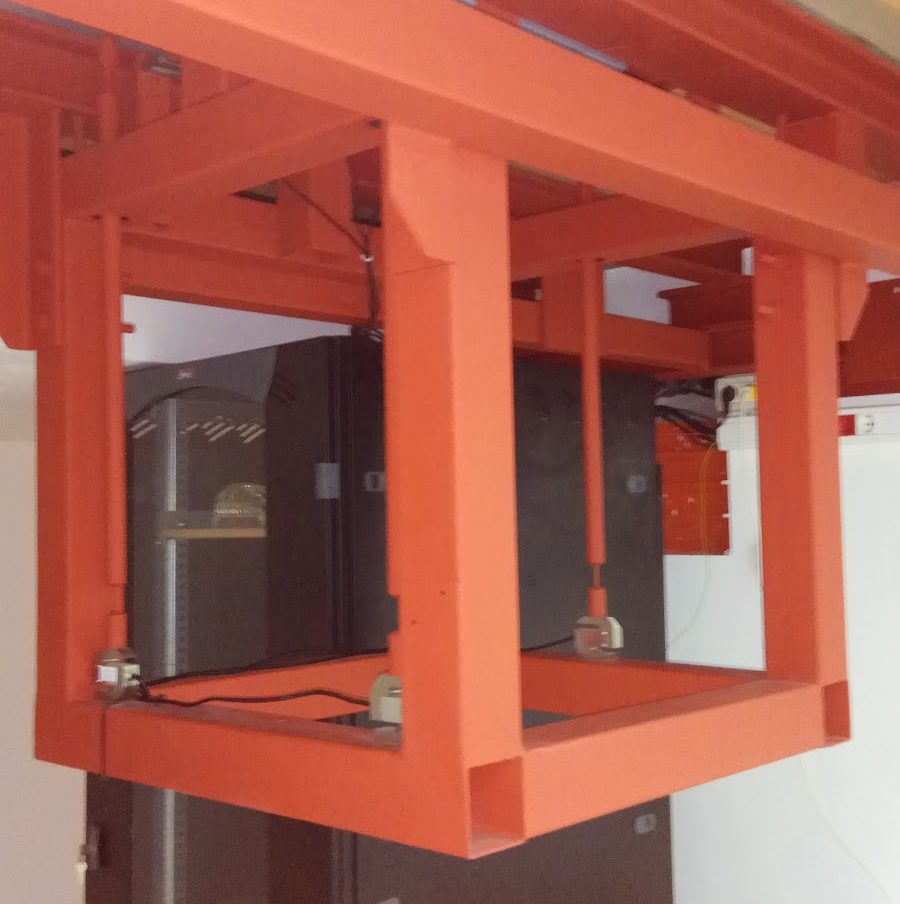
Imagen 4. Balanza del túnel de viento de ITER.
Por otra parte se revisan y ponen en marcha los sensores que permiten conocer en tiempo real los parámetros necesarios para determinar las condiciones del ensayo: velocidad del aire, temperatura, presión dinámica, etc. En algunos casos es necesario instrumentar el modelo, añadiendo tomas de presión sobre la superficie de este para poder medir no solo las fuerzas aplicadas sobre el modelo, sino también cómo éstas se manifiestan sobre la superficie.
Cuando se realiza una nueva campaña con un modelo nuevo, es necesario calibrar el túnel, que consiste en reajustar los diferentes sensores respecto al nuevo modelo instalado. Si no se hiciera esto, los datos recogidos no serían del todo correctos, ya que podrían tener interferencias y acoplamientos entre ellos. Para la calibración se suelen realizar ensayos puntuales y una vez obtenidos los resultados se calcula una función de corrección la cual se aplica en el software de control para eliminar así los errores.
Operación
Una vez montado el modelo y realizada toda la calibración del sistema, es hora de empezar con el plan de ensayos. Para ello se emplea un software de desarrollo propio el cual es capaz de transformar todos los datos recibidos por los medidores de fuerza (galgas) y los sensores de temperatura, velocidad y ángulo instalados dentro de la cámara.
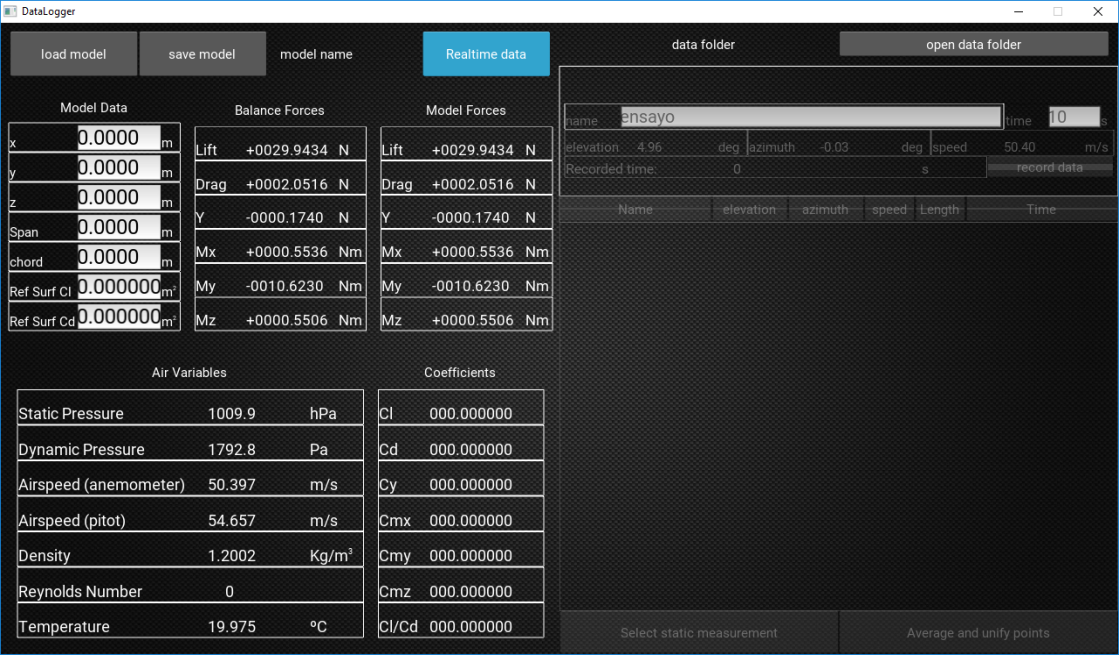
Imagen 5. Software de control y operación del túnel de viento de ITER.
Este software de control permite monitorizar los parámetros del ensayo en tiempo real, una vez caracterizado el modelo a ensayar. Además de la monitorización, el software permite operar de manera remota los parámetros de los ventiladores, actuadores, etc… modificando así la velocidad del túnel así como el ángulo del modelo a ensayar en tiempo real. Cada vez que se realiza una prueba se genera un archivo de resultados donde se vuelcan todos los datos de cada ensayo puntual y una vez se completan se unifican estos datos creando un nuevo fichero resumen, así como una gráfica de los mismos para facilitar su interpretación.
Completadas todas las pruebas descritas en el plan de ensayos, se recopilan los resultados y se entregan al cliente, el cual procesa y analiza en detalle sacando las conclusiones pertinentes. Es frecuente usar el resultado de los análisis en túnel de viento para afinar los algoritmos utilizados en los análisis de fluido computacionales (CFD).
Puede consultarse más información sobre la realización de ensayos en el Túnel de Viento en https://www.iter.es/portfolio-items/ensayos-en-tunel-de-viento/